Investigating Hazardous Occurrences
Adverse events have many causes. What may appear to be bad luck can, on analysis, be recognized as a chain of failures and errors that lead almost inevitably to the hazardous occurrence event. These causes can be classified as:
immediate causes – the agent of injury or ill health (the blade, the substance, the dust etc.);
underlying causes – unsafe acts and unsafe conditions (the guard removed etc.);
root causes – the failure from which all other failings grow, often remote in time and space from the adverse event (failure to identify training needs and assess competence, low priority given to risk assessment etc.).
To prevent adverse events, you need to provide effective risk control measures which address the immediate, underlying and root causes.
There are hazards in all workplaces; risk control measures are put in place to reduce the risks to an acceptable level to prevent accidents and cases of ill health. The fact that an adverse event has occurred suggests that the existing risk control measures were inadequate. Learning lessons from near misses can prevent costly accidents. While the argument for investigating accidents is clear, the need to investigate near misses and undesired circumstances may not be so obvious. However, investigating near misses and undesired circumstances is as useful as investigating accidents.
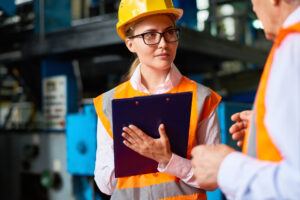
An investigation is the first step in preventing future hazardous occurrences. A good investigation will enable you to learn general lessons, which can be applied across your organization. The investigation should identify why the existing risk control measures failed and what additional measures are needed.
Simply dealing with the immediate causes of an adverse event may provide a short-term fix, but, in time, the underlying root causes that were not addressed will allow conditions to develop where further adverse events are likely, possibly with more serious consequences. It is essential that the immediate, underlying causes and root causes are all identified and remedied.
Investigations should be conducted with accident prevention in mind, not placing blame. Investigations that conclude that worker error was the sole cause are rarely acceptable. Underpinning the ‘human error’ there will be several underlying causes that created the environment in which human errors were inevitable. For example, inadequate training and supervision, poor equipment design, lack of management commitment, poor attitude to health and safety.
The objective is to establish not only how the adverse event happened, but more importantly, what allowed it to happen.