Crystaline Silica Exposure
Occupational regulations for silica dust outline the required elements and considerations such a risk assessment, exposure control plans, air monitoring, record keeping, house keeping practices, and worker instruction and training. Workers are not to engage in a work activity or a silica process that may result in exposure to (RCS) respirable crystaline silica dust unless […]
Read More →Safety Headgear / Hard Hats
Under the Occupational Health and Safety Regulation, “safety headgear must be worn by a worker in any work area where there is a danger of head injury from falling, flying or thrown objects, or other harmful contacts.” Hard hats need to comply with Type I and II top and lateral impact CSA Z94.1-2005 (Class E), […]
Read More →Fall Arresters & Vertical Lifelines
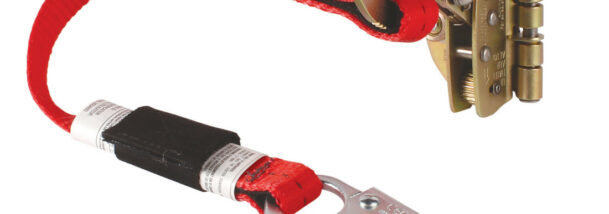
The new CSA Z259.2.5-17 Fall Arresters and Vertical Lifelines came into effect on June 1, 2019 and supersedes the previous 2012 edition. Rope Grabs must now be manufactured to meet the requirements of the new CSA standard. The new 2019 CSA standard now requires manufacturers to make a 76.2 cm (30 in.) lanyard integral to […]
Read More →Fall Protection Harnesses
If you are at risk for falling three metres (10 feet) or more at your workplace, you should wear the appropriate fall protection equipment. If fall protection is required, establish a complete fall protection program if one is not in place. The program should include educating and training workers, selecting and fitting the equipment for […]
Read More →Focus on Eye and Face Protection
The Occupational Health and Safety Regulation provides for Eye and Face Protection. If your work exposes your eyes to hazards such as dust or chemicals, or to the risk of impact with tools, materials, or flying debris, occupational guidelines stipulate that you must wear safety eyewear. You also need to be aware that regular prescription […]
Read More →Hand & Arm Protection
If a workplace hazard assessment reveals that workers face potential injury to hands and arms that can’t be eliminated through engineering and work practice controls, employers must ensure that employees wear the appropriate protection. Potential hazards include chemical or thermal burns, electrical dangers, bruises, abrasions, cuts, punctures, fractures and amputations. Protective equipment includes gloves, finger […]
Read More →Hearing Protection Devices
According to the Occupational Health and Safety Regulation and Guidelines, employers are required to provide hearing-loss prevention programs, monitor noise levels and conduct annual hearing tests for workers exposed to hazardous noise levels to prevent permanent hearing damage. Hazardous noise levels are defined as 85 decibels in the A scale for eight hours or the […]
Read More →Protective Clothing
The various methods to control risks are, in order of preference, hazard elimination, substitution, engineering controls, administrative controls and personal protective equipment (PPE). Workers are responsible for providing basic safety head gear such as a hard hat, hand protection, safety footwear and clothing appropriate for the weather. Employers are responsible for providing any additional PPE […]
Read More →Fire Watch & Fire Extinguishers
A fire watch is implemented to ensure the fire safety of a building or area in the event of any hot work, or situation that may pose increased risk to persons or property. The term “Fire Watch” is used to identify a procedure for the detection of fire by designated persons. Canadian occupational regulations stipulate […]
Read More →Spill Containment and Clean-up
Spills can occur during fuelling, handling chemicals or due to mechanical failure of equipment. It is important to conduct hazard assessments at your worksite to identify spills and get them cleaned-up. Monitoring for staining can be added to the inspection checklist and spill trays should be used when employees are refuelling equipment as any drips, […]
Read More →