Toolbox Talks
Toolbox talks are short, instructional safety sessions and are usually held daily at the start of a shift. A toolbox talk can improve safety compliance by reminding workers about compliance requirements and by helping workers recognize the importance of following compliance rules to protect their personal safety. Most talks last about 20 minutes and include the following:
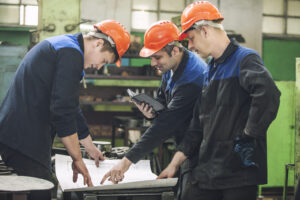
- Work periods are identified and reviewed.
- Hazard and risks that potentially may be encountered that day.
- Safety reminders and quick safety lessons on topics that need to be refreshed.
- Changes to work procedures or job scope are communicated and
- New crew members or anyone that was not at the initial pre-job general safety meeting can be brought up to speed.
A good toolbox talk gets employees thinking and talking about safety.
When employees are engaged in safety, they exhibit positive safety behaviours, such as wearing personal protective equipment without being asked and that can be of great benefit to an organization safety culture.
Safety culture embodies the value placed on safety and the extent to which people take personal responsibility for safety within an organization. Safety culture is often described as the personality of an organization, as it is a shared value of safety.
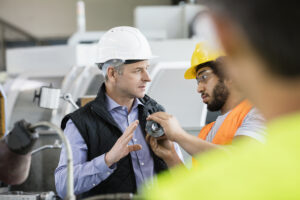
Safety leadership must be demonstrated and is often argued to be the single most influential factor of safety culture. A toolbox talk can deliver experienced based safety tips which enhances understanding and better prepares workers to deal with safety challenges while performing their job tasks. Toolbox talks can strengthen work relationships that last well into the future.
It can be a challenge to write toolbox talks and that is why more and more OHS Registry members are turning to the OHS Registry for quality toolbox talks.
We have FREE toolbox talks that you can download right into your computer.
A new toolbox talk will be published on this site each month. Each topic selected is generic enough to be applied to many different work environments. While the information contained in each toolbox talk is thought to be accurate, these toolbox talks are not intended to take the place of formal OHS Registry training. They all come with a sign-in sheet you can use to document the toolbox talk and keep on file to demonstrate your on-going commitment to workplace safety.
Recent Toolbox Talks
12-19 - Crystaline Silica Exposure
Occupational regulations for silica dust outline the required elements and considerations such a risk assessment, exposure control plans, air monitoring, record keeping, house keeping practices, and worker instruction and training. Workers are not to engage in a work activity or a silica process that may result in exposure to (RCS) respirable crystaline silica dust unless a risk assessment has first been completed by a qualified person.
Silica is a designated substance requiring employers to keep exposures as low as reasonably achievable (ALARA). Silica makes up nearly all of what we call âsandâ and ârock.â Silica may occur as amorphous free silica and crystalline free silica, of which the three principal forms are quartz, tridymite and cristobalite. Certain materials contain both amorphous and crystalline free silica.
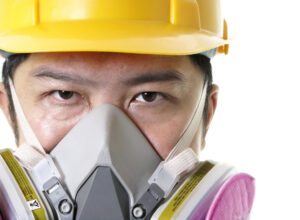
Most of the products sold for industrial use are termed silica sand. The silica in the sand will normally be in the crystalline free silica form of quartz. Some common materials that contain silica include rock and sand, topsoil and fill, concrete, cement, mortar masonry, brick, tile, granite, sandstone, slate, asphalt that contains rock and stone) and fibrous cement board containing silica.
Silica is a primary component of construction materials, and silica containing dust can be generated from cutting, grinding, sanding, sandblasting, drilling or abrasive blasting, on concrete, bricks or masonry blocks. Particles, known as the respirable fraction, are the cause of silica-related diseases. These particles are so small that individually they cannot be seen and are capable of penetrating to the area of the lung in which gas exchange occurs. When work tasks create silica containing dust, the process can be enclosed and venting points connected to local exhaust ventilation can be implemented. In other applications such as cutting operations, wetting may be more effective than local exhaust ventilation. Respirators should not be relied on as a primary means of preventing exposure to silica dust. If a worker is or might be exposed in a workplace to an air contaminant that exceeds an 8-hour TWA the worker must wear an appropriate respirator. Respirator which requires an effective seal with the face for proper functioning necessitates the worker undergoing annual fit testing to demonstrate that the facepiece forms an effective seal.
11-19 - Safety Headgear / Hard Hats
Under the Occupational Health and Safety Regulation, âsafety headgear must be worn by a worker in any work area where there is a danger of head injury from falling, flying or thrown objects, or other harmful contacts.â Hard hats need to comply with Type I and II top and lateral impact CSA Z94.1-2005 (Class E), ANSI/ISEA Z89.1-2009 (Class E) standard. Your hard hat has a label of certification on the inside of the hard hat shell.
Type I Hard Hats are intended to reduce the force of impact resulting from a blow only to the top of the head.
Type II Hard Hats are intended to reduce the force of lateral impact resulting from a blow received off-centre, from the side, or to the top of the head.
Hard hat electrical performance is divided into 3 categories: Class E, Electrical; Class G, General, and; Class C, Conductive.
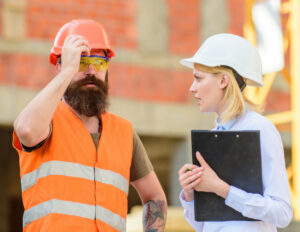
Discussion What a Hard Hat Does
- Protects you from falling objects.
- Protects your head in case of a fall or bumpâs into machinery and the like. It also protects you from electrical shocks and burns if itâs a non-conductive hat.
- It is a place to put stickers and decals.
Proper Care for your Hard Hat
- Keep your hard hat properly adjusted.
- Do not cut, bend or heat the hard hat.
- If you see gouges or cracks in the shell, or the colour turns dull, its time for a new one.
Proper Wear
- Most importantly, wear it and wear it correctly. Do not wear it backwards.
- Do you need lateral or side protection. Donât put anything inside except your head.
- Do you need a chin strap in order to keep it on your head.
- Donât try to substitute it for a âbump cap.â The bump cap will not provide adequate protection from falling objects.
- It is not a stool or a step; doing so weakens the shell of the hard hat.
10-19 - Fall Arresters & Vertical Lifelines
The new CSA Z259.2.5-17 Fall Arresters and Vertical Lifelines came into effect on June 1, 2019 and supersedes the previous 2012 edition. Rope Grabs must now be manufactured to meet the requirements of the new CSA standard.
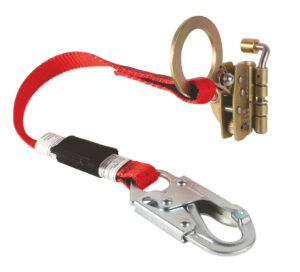
The new 2019 CSA standard now requires manufacturers to make a 76.2 cm (30 in.) lanyard integral to the Rope Grab unit. In the 2012 version of the standard, the requirement of the 76.2cm (30in.) or less lanyard was there, but the lanyard did not have to be made integral to the rope grab itself.
Rope grabs should always be matched to the lifeline this will ensure the mobility of the rope grab along the lifeline. A rope grab used with an incompatible lifeline could prevent the rope grab from being pulled along while a worker is climbing. All Rope grabs and vertical lifelines are CSA certified together as a pair. By mixing manufactures, the CSA certification becomes void. Simply put the rope grab might not function properly on a lifeline that was not matched to the rope grab when it was manufactured.
Although the 2012 standard did advise workers to use a lanyard that was less than 76.2cm (30in.) when used with a rope grab and vertical lifeline, lots of workers continued and still continue to use a 1.83 metre (6 foot) lanyard. The risk when using a 1.83 metre (6 ft) lanyard with an automatic rope grab is that there is a risk of a potential free fall that can be 3 to 3.6 metres (10-12 ft) if the trailing rope grab is positioned near the users feet when a fall occurs. This situation is likely to occur during work tasks that involve roofing applications. It is important to keep in mind that even though the lanyard has a built in energy absorber the product would not have been designed to sustain arresting forces created by a free fall of 3 to 3.6 metres (10-12 ft). Manufacturers are now required to design in the correct 76.2cm (30in.) length limit. The design will ensure that a workerâs free fall distance will remain within the products design parameters.
09-19 - Fall Protection Harnesses
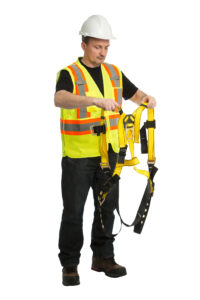
If you are at risk for falling three metres (10 feet) or more at your workplace, you should wear the appropriate fall protection equipment.
If fall protection is required, establish a complete fall protection program if one is not in place. The program should include educating and training workers, selecting and fitting the equipment for the task and the worker, and knowing how to inspect the equipment.
The requirements for full body harnesses fall under the CSA standard CAN/CSAZ259.10. The standard specifies design, testing, marking, and information requirements for use of full body harnesses intended for use as body supports in personal fall arrest systems and in other work situations that involve the risk of falling.
Classification of full body harnesses:
- Class A: Fall Arrest (Back D-ring)
- Class D: Suspension & Controlled Descent (Front Lower D-ring)
- Class E: Limited Access/Extrication (Shoulder D-rings)
- Class L: Ladder Climbing (Front upper D-ring)
- Class P: Work Positioning (Side D-rings)
It is important to follow directions when it comes to ensuring a snug fit with chest, back D-ring and leg straps. In many instances, workers wear harnesses far too loose. It is very important that chest straps are positioned in the mid-chest area, and back D-rings located in the middle of the back between the shoulder blades. Both must be tightened for a âsnugâ fit. Chest straps should be easy to adjust, but must withstand fall forces without tearing or breaking during a fall. If a chest strap is not fastened properly, it can slide up around a workerâs neck after a fall. Some workers are relying on a universal sizing on their harness that are manufactured to fit almost everyone. To accommodate all employee shapes and sizes, some manufacturers now offer dozens of styles and designs developed specifically to meet the needs of the individual worker.
08-19 - Focus on Eye and Face Protection
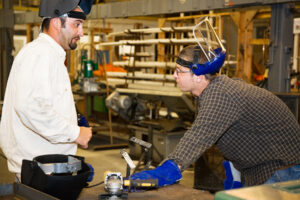
The Occupational Health and Safety Regulation provides for Eye and Face Protection. If your work exposes your eyes to hazards such as dust or chemicals, or to the risk of impact with tools, materials, or flying debris, occupational guidelines stipulate that you must wear safety eyewear. You also need to be aware that regular prescription glasses or contact lenses are not a substitute for safety eyewear and if you work in dry, dusty, or chemically charged environments, contact lenses may not be suitable, even when worn with safety eyewear.
Safety glasses provide minimum protection and are for general working conditions.
Goggles provide higher impact and acid or chemical splash protection.
Face shields protect the full face from injury and they offer the highest impact protection from spraying, chipping, grinding and chemicals, however a face shield is considered a secondary safeguard to protective eyewear, it should not be worn without safety glasses or goggles.
The Canadian National Institute for the Blind (CNIB) report that every day, 700 Canadian workers sustain eye injuries on the job, often resulting in lost time and, in some cases, temporary or permanent vision loss.
Employers need to set up first-aid procedures for eye injuries and have eyewash stations that are easy to get to and supervisors need to conduct safety talks to highlight the need for protective eyewear. The professionals at the OH&S Safety Registry know that sight is one of our most precious senses and the ability to observe the world around us depends on it.
Protect your eyes by wearing protective eyewear that fits well, is comfortable and suited to the job.
07-19 - Hand & Arm Protection
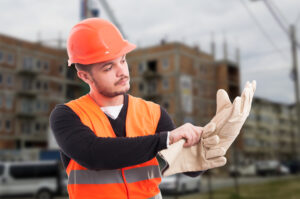
If a workplace hazard assessment reveals that workers face potential injury to hands and arms that canât be eliminated through engineering and work practice controls, employers must ensure that employees wear the appropriate protection. Potential hazards include chemical or thermal burns, electrical dangers, bruises, abrasions, cuts, punctures, fractures and amputations. Protective equipment includes gloves, finger guards and arm coverings. There are many types of gloves available today to protect against a wide variety of hazards. Assessing the nature of the hazard and the operation involved will provide direction toward selecting the right gloves. It is essential that workers use gloves specifically designed for the hazards and tasks found in their workplace because gloves designed for one function may not protect against a different function.
Factors that may influence the selection of protective gloves for a workplace include the type of chemicals being handled, the nature of contact (total immersion, splash, etc.), the duration of the contact, the area requiring protection (hand only, forearm, full arm length), grip requirements, thermal protection and abrasion resistance requirements.
- Leather gloves protect against sparks, moderate heat, blows, chips and rough objects.
- Aluminized gloves provide reflective and insulating protection against heat and require an insert made of synthetic materials to protect against heat and cold.
- Aramid fiber gloves protect against heat and cold, are cut- and abrasive-resistant and wear well.
- Synthetic gloves of various materials offer protection against heat and cold, are cut- and abrasive-resistant and may withstand some diluted acids. These materials do not stand up against alkalis and solvents.
Protective gloves should be inspected before each use to ensure that they are not torn, punctured or made ineffective in any way. A visual inspection will help detect cuts or tears and any gloves with impaired protective ability should be discarded and replaced.
06-19 - Hearing Protection Devices
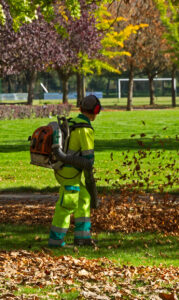
According to the Occupational Health and Safety Regulation and Guidelines, employers are required to provide hearing-loss prevention programs, monitor noise levels and conduct annual hearing tests for workers exposed to hazardous noise levels to prevent permanent hearing damage. Hazardous noise levels are defined as 85 decibels in the A scale for eight hours or the equivalent; the A scale is used for measuring environmental noise. All workers are responsible for wearing appropriate hearing protection and taking part in their employerâs hearing-loss prevention program. Since 2006 there have been more than 41,000 accepted claims for noise induced hearing loss (NIHL) in British Columbia.
Employers can take measures to prevent noise induced hearing loss:
- Ensure all workers who are at risk are wearing sufficient hearing protection that fits, and that they understand how to properly wear it.
- Make sure workers insert or wear the correct hearing protection prior to entering a noisy environment and wear it until after exiting the noisy location.
- Rotate workers to different positions so they spend less time in noisy environments.
- Identify potential engineering controls to mitigate risk of exposure.
- Ensure workers have their hearing tested and are aware of their hearing-test results.
Hearing protection devices are effective against noise exposure from chop saws, chain saws, circular saws, routers, screw gun, drills, pneumatic nail guns and other power tools. Where communications with co-workers is critical worker can wear protection that does not block out too much noise â custom earplugs with vents, earplugs with a connecting cord, class B earplugs or earmuffs and electronic earmuffs or earplugs.
05-19 - Protective Clothing
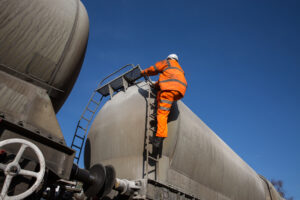
The various methods to control risks are, in order of preference, hazard elimination, substitution, engineering controls, administrative controls and personal protective equipment (PPE). Workers are responsible for providing basic safety head gear such as a hard hat, hand protection, safety footwear and clothing appropriate for the weather. Employers are responsible for providing any additional PPE required for the job, at no cost to the worker and may include high-visibility apparel, respiratory protection, fire-resistant clothing, noise face or body protection. PPE needs to be properly selected, used, and maintained to be effective. PPE selection and use should be based on a risk assessment. Consider applicable standards for the type of PPE and could it create any additional hazards.
Flame-resistant (FR) clothing is a must for any occupations that put workers at risk of burns from hydro carbon flash fires and electric arcs. The first step in choosing the right PPE for the job is identifying the hazard, whether itâs flash fire or electric arc flash. The best type of fabric choice is one that self-extinguishes quickly (the longer a fabric can burn, the more likely it is to burn the wearers skin). The garmentâs flame-resistant properties ensure it will resist catching fire, and if it does catch fire, it will not continue to burn once the source of combustion is removed.
Flame-resistant (FR) clothing can and will burn when introduced to open flame from a flash fire, arc flash, combustible dust explosion or other fire sources. Flame-resistant clothing is NOT fireproof. All Arc Rated (AR) clothing is flame resistant (FR), but not all Flame-resistant clothing has been Arc Rated. By not continuing to burn after the initial hazard is over, FR clothing limits burn injury to, at most, only the body surface area directly impacted by the hazard. All Arc Rated clothing is flame resistant; the official arc rating standard requires fabrics to be subjected to arc flash testing. Arc rating is defined as the amount of energy a given fabric can withstand before a 50 percent likelihood of the onset of second degree burn through the fabric. In other words, what is being measured is insulation of FR fabrics to arc flash. The arc rating is reported as a single number and the higher the better.
04-19 - Fire Watch & Fire Extinguishers
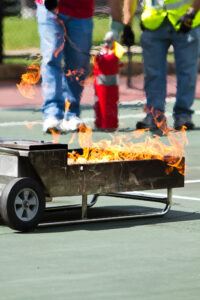
A fire watch is implemented to ensure the fire safety of a building or area in the event of any hot work, or situation that may pose increased risk to persons or property.
The term âFire Watchâ is used to identify a procedure for the detection of fire by designated persons. Canadian occupational regulations stipulate that the employer is responsible for ensuring workers involved in hot work operations have received adequate instruction and that fire watch workers have demonstrated competency in the use of a portable fire extinguisher.
Only workers who have been trained in the recognition and avoidance or hazards and the safe use of a portable fire extinguisher may perform fire watch tasks.
Any time an assessment by the workers supervisor reveals any gaps in the workerâs knowledge or skills, the employer needs to ensure these gaps are addressed through further training and instruction. The fire watch has the responsibility to make certain the hot work area is maintained in a fire-safe condition throughout performance of the hot work and has the authority to stop the hot work if unsafe conditions are observed.
Training will help to ensure that fire watch workers understand what their responsibilities are and that they are proficient in the use of a portable fire extinguisher.
- Make sure you know the limitations & proper use of A, B, C and D fire extinguishers
- Make sure you know which type of fire extinguisher to use on each type of fire
- Make Sure you know how to use the right fire extinguisher to fight a small fire
- If the fire is to large to control call 911 and activate the emergency response plan
03-19 - Spill Containment and Clean-up
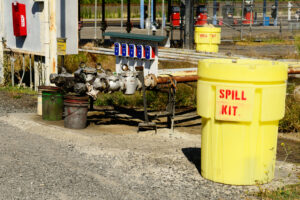
Spills can occur during fuelling, handling chemicals or due to mechanical failure of equipment. It is important to conduct hazard assessments at your worksite to identify spills and get them cleaned-up.
Monitoring for staining can be added to the inspection checklist and spill trays should be used when employees are refuelling equipment as any drips, or spills can be quickly absorbed into the ground, or easily create a slip trip and fall hazard on an otherwise safe concrete floor.
Cleaning up a workplace fuel spill or controlling a fuel spill from spreading on the ground may only require the use of absorbent socks found in spill kits. Hazardous waste containers are a must have item to place fuel socked absorbent socks into until they can be properly disposed of. It is important to take the necessary precautions to protect against spills, along with creating a plan for containing and cleaning up a fuel spill should it occur.
To help you deal with the dangers of a workplace spill Universal Spill Kits are available so that you can take on the widest range of liquids. They are made to handle the kind of liquids that you use most, like water, oils, solvents or coolants. The universal containers are perfectly packed for fast response to keep you and your employees prepared from one end of your job site to the other.
In addition, Vehicle Spill Response Kits are available and in stock that are ideal for carrying in the cab of your truck. The compact vehicle response kit fits behind the seat in most truck cabs and has everything needed to handle small spills while you are on the road. Be prepared, donât get caught without a spill response kit.
- Promote a discussion on the topics covered in the Tool Box Talks. Should any question arise that you cannot answer, donât hesitate to contact your Supervisor.
Talk to Us!
Canada West: (778) 957-6407
Canada East: (647) 250-7646
Mail Us!
Send Postal Mail To:
OH&S Registry
825B Laval Crescent
Kamloops, BC V2C 5P2
Canada